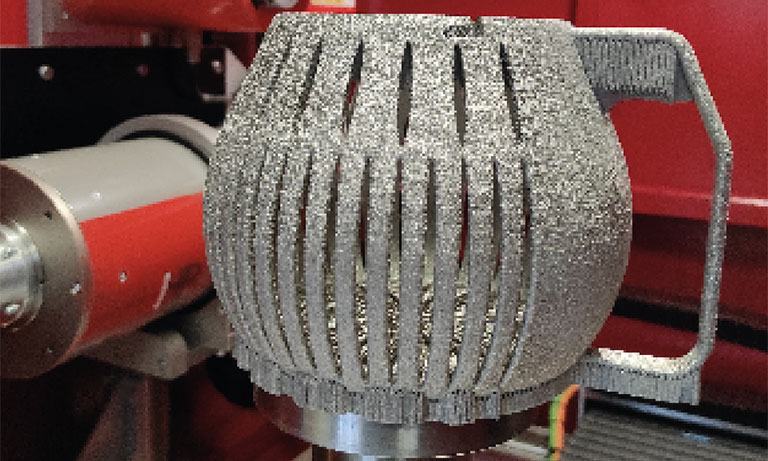
L'intelligenza artificiale a supporto della manifattura additiva
DOI 10.12910/EAI2025-015
di Giovanni Di Girolamo, Giuseppe Barbieri Dipartimento Sostenibilità, circolarità e adattamento al cambiamento climatico dei Sistemi Produttivi e Territoriali, Divisione Tecnologie e materiali per l’Industria Manifatturiera Sostenibile - ENEA
La produzione additiva intelligente nasce dall’integrazione di manifattura additiva e intelligenza artificiale: l’intero processo è gestito in real-time, dal design all’esecuzione della stampa, dal monitoraggio della qualità alla manutenzione delle apparecchiature.
L’intelligenza artificiale (IA) è la capacità di una macchina di simulare l’intelligenza umana, analizzando ed elaborando una grande mole di dati complessi in tempi brevi, a supporto dei processi decisionali. Sistemi fondati su apprendimento automatico di modelli matematici adattano il proprio comportamento analizzando gli effetti prodotti dalle azioni precedenti e operando in autonomia. Le metodologie di IA hanno una percezione dell’ambiente di lavoro nella sua complessità, elaborano dati e informazioni mediante raccolta e interpretazione di input, apprendono, intraprendono azioni correttive, mantengono controllo e accessibilità dei dati. Il loro uso è giustificato da crescenti esigenze industriali in materia di automazione di processi, analisi di big data, prevenzione.
Il machine learning (ML) utilizza algoritmi per identificare modelli e generare soluzioni, mentre il deep learning (DL) si fonda su algoritmi di reti neurali (NNs), inspirate da struttura e funzioni del cervello, costituite da nodi interconnessi atti a processare e trasmettere dati e informazioni, permettendo al sistema di riconoscere i modelli, fare previsioni a partire dai dati iniziali e prendere decisioni in real-time. Esse consentono di analizzare e ottimizzare processi di manifattura complessi: possono gestire relazioni non lineari, operare in ambienti dinamici come linee di produzione, adattarsi a nuovi dati, continuando ad apprendere e migliorando la performance. Sono state utilizzate per sviluppare modelli che utilizzano dati storici e correnti per predire futuri comportamenti della linea, anticipando criticità tali da rallentare o arrestare la produzione.
Esistono casi studio industriali su implementazione della IA nell’ottimizzazione della pianificazione, nella modellizzazione e ottimizzazione dei parametri produttivi, nel rilevamento di difetti in tempo reale, nella previsione della performance di macchina, nel riconoscimento delle azioni degli assemblatori.
Benefici e prospettive
Nella manifattura additiva (MA) il componente è prodotto a partire da un modello CAD, fondendo il materiale (polvere, filamento, pellet) e depositandolo strato per strato, per applicazioni che vanno dalla produzione di massa alla produzione in piccoli volumi di parti customizzate, in vari settori: biomedicale (impianti, protesi, scaffold); aerospaziale (parti di velivoli e satelliti), elettronico, energia/trasporti (microturbine, dischi freno, cuscinetti, valvole). La crescente diffusione della tecnologia è dovuta a vantaggi economici e tecnologici. L’ottimizzazione di design, processo e relativi parametri consente di realizzare componenti complessi con specifiche caratteristiche geometriche e prestazionali, a più elevata funzionalità rispetto agli analoghi prodotti con metodi tradizionali, di ridurre consumo di materiale e scarti, incrementando efficienza e produttività. In ottica digitalizzazione e automazione, le aziende spingono per soluzioni basate su cloud che integrino vari algoritmi e ottimizzino l’intera catena.
Il ML si utilizza per analizzare e ridefinire lo stato della produzione. Per definire un modello/algoritmo adeguato a raccolta ed elaborazione dei dati, occorre individuare i parametri chiave e integrare i dispositivi di misura, considerando le connessioni esistenti fra le fasi di processo.
La IA può valutare se la MA è la tecnologia più efficace ed efficiente per realizzare e validare un dato design. Il suo potenziale è nella facilità e rapidità nel produrre varianti di design intelligenti basate su variabili predefinite, su un set di parametri (proprietà dei materiali, spessore layer, orientamento della stampa, strutture di supporto) e requisiti tecnici.
Il design generativo guidato da algoritmi di ML genera in tempi brevi geometrie complesse e innovative, a volte impossibili da realizzare con metodi tradizionali, minimizzando le iterazioni e replicando il processo di simulazione di un componente prima di produrlo, così riducendo tempi e costi. Nell’ambito del progetto INSPIRATION la divisione Tecnologie e materiali per l’Industria Manifatturiera Sostenibile dell’ENEA studia l’alleggerimento di componenti aeronautici mediante il design con geometrie trabecolari e giroidiche ottimizzate.
Il ML si applica all’ottimizzazione topologica, dell’uso di materiale e dell’integrità strutturale, come dimostrato nella produzione di componenti leggeri ad elevate resistenza meccanica e performance (GE Aviation/Airbus).
Il ruolo della IA nell’assicurazione di qualità e nel rilevamento dei difetti
Nel processo di stampa 3D, una volta definite la qualità dei materiali e la geometria dei componenti, vengono fissati i relativi valori di verifica. Le macchine per stampa 3D sono profondamente sensorizzate e, quindi, in grado di fornire una quantità notevole di dati (storici e attuali) per l’istruzione della IA che, analizzandoli in real-time, permette azioni tempestive nel caso in cui escano fuori soglia. Ciò compete ad algoritmi di ML atti a sviluppare il modello. Notevole è il ruolo della IA nell’assicurazione di qualità e nel rilevamento dei difetti.
Sistemi di IA assistono gli operatori della linea di produzione nel controllo in real-time dei componenti mediante sistemi di visione e monitoraggio, al fine di individuare eventuali difetti strutturali, correlarli ad anomalie di processo e intervenire senza attendere l’ispezione a fine ciclo, così evitando la produzione di scarti. Ciò consente di ottimizzare il consumo di materiale e il processo di stampa, migliorando la produzione.
Per avere previsioni attendibili le tecnologie di IA basate su approcci data-driven vanno integrate con i modelli fisici [2]. Il digital twin è la rappresentazione virtuale del processo fisico, che ha un impatto su design, simulazione di processo, predizione della performance, retroazione. Con questo si intende l’utilizzo dei dati reali nel digital twin, al fine di ottimizzare accuratezza e capacità predittive. EOS ha sviluppato un digital twin per il processo di stampa DMLS (Direct Metal Laser Sintering): le immagini termiche (tomografia ottica) di ogni strato stampato sono confrontate con l’immagine generata da IA, in caso di anomalia (mancanza di polvere, difetti di ricopertura del singolo strato), il processo si arresta.
Nella MA metallica le caratteristiche del bagno di fusione determinano caratteristiche e qualità del componente. Monitorarle in tempo reale, individuare e correggere tempestivamente deviazioni dei parametri dai valori ottimali, riportandoli entro i limiti, previene la produzione di difetti. Con il controllo dello spessore del layer, dell’orientamento di stampa, delle strutture di supporto si può ottimizzare la strategia di scansione, senza tralasciare le successive operazioni (rimozione dei supporti, trattamento termico, finitura superficiale) [3].
Analisi predittive, miglioramento della qualità e catena del valore
Reti neurali sono state impiegate per l’analisi predittiva nella modellazione, onde stabilire la correlazione tra parametri (temperatura, lunghezza del bagno) e proprietà dei componenti stampati [4,5]. Il modello è stato ottimizzato per ricavare previsioni accurate su velocità del laser, distribuzione di temperatura, geometria finale dell’interfaccia gas/metallo.
Ford ha utilizzato la IA per migliorare qualità dei componenti stampati e sicurezza dei passeggeri. BMW ha impiegato la progettazione guidata per fabbricare componenti leggeri in metallo. Nel settore biomedicale tessuti e organi stampati con l’ausilio della IA aprono le porte alla medicina rigenerativa.
L’impiego della IA impatta sull’intera catena del valore, comprese le fasi successive alla stampa. AUTOMAT3D (Post Process) è un software di post elaborazione in grado di gestire operazioni automatizzate, come rimozione del supporti, di resina e polvere, o la finitura superficiale dei componenti.
Il monitoraggio dello stato e la diagnosi della vita residua delle macchine mediante sensori intelligenti sono le basi della manutenzione predittiva, con cui si ottimizza l’uso delle stampanti, pianificando i tempi di manutenzione. Stanno comparendo sistemi di esecuzione della manifattura (MES) in grado di gestire stampanti, inventario e operazioni post stampa, vista l’esigenza di massimizzare l’efficienza dell’intera linea.
In sintesi, si possono identificare quattro tecnologie [6]:
- metodi e strumenti digitali costituenti l’infrastruttura per design e piano di produzione;
- sistemi di controllo e sensoristici avanzati;
- algoritmi a supporto delle decisioni uomo-macchina;
- modellizzazione e ottimizzazione del design.
Conclusioni
L’integrazione della IA nei processi di manifattura additiva ha un alto potenziale. L’utilizzo di algoritmi di ML/DL basati su reti neurali semplifica la fase di design e simulazione della produzione, consente monitoraggio e controllo del processo di stampa in real-time, ottimizzando il consumo di materiale e rilevando anomalie di processo in tempo reale, intervenendo tempestivamente per mantenere il processo sotto controllo e migliorando l’efficienza di linea, a beneficio della qualità dei prodotti, di tempi e costi, così riducendo il time-to-market. La IA è di supporto alla manutenzione predittiva. Nell’ottica di integrare soluzioni che ottimizzino l’intera catena, ulteriori benefici possono scaturire da: tecnologie di automazione che facilitino gli assemblaggi, migliore integrazione dei processi fisici con metodi di IA, trasparenza, interpretabilità e affidabilità dei dati prodotti dalla IA.
Bibliografia
[1] ENEA-PROMAS, “Relazione tecnica sull’andamento del progetto INSPIRATION – Integrate and Sustainable PRocesses and mAterials for smaRT ON demand laser additive manufacturing”, Stato di avanzamento n.7 (2023), 1-147.
[2] X. Xie, J. Bennett, S. Saha, Y. Lu, J. Cao, W.K. Liu, Z. Gan (2021), “Mechanistic Data-Driven Prediction of As-Built Mechanical Properties In Metal Additive Manufacturing”, npj Computational Materials,7 (1), 1-12.
[3] N. Kladovasilakis, P. Charalampous, I. Kostavelis, D. Tzetzis, D. Tzovaras (2021), “Impact of Metal Additive Manufacturing Parameters on the Powder Bed Fusion and Direct Energy Deposition Processes: A Comprehensive Review”, Progress in Additive Manufacturing,6, 349-365.
[4] S. Liao, T. Xue, J. Jeong, S. Webster, K. Ehmann, J. Cao (2023),“Hybrid Thermal Modeling of Additive Manufacturing Processes Using Physics-Informed Neural Networks for Temperature Prediction and Parameter Identification”, Computational Mechanics, 72, 499-512.
[5] Q. Zhu, Z. Liu, J. Yan (2021), “Machine learning for metal additive manufacturing: predicting temperature and melt pool fluid dynamics using physics-informed neural networks”, Computational mechanics, 67, 619-635.
[6] Y. Xiong, Y.Tang, Q. Zhou, Y. Ma, D.W. Rosen (2022), “Intelligent additive manufacturing and design: state of the art and future perspectives”, Additive Manufacturing, 59, 103139.